Meridian Contracting is saving time and gaining flexibility with the concrete forms it uses to pour parapets on box culverts for highway renovation and reconstruction projects. The metal parapet forms are designed so the company can use them for either single- or double-slope parapets (wall barriers) with minor adjustments.
Meridian Engineering Company, dba Meridian Contracting, Inc., was founded in 2003 and is owned by Ted Haworth and Mark Sutton. The firm specializes in bridge work, concrete work, utilities and related public works projects throughout New Mexico, Arizona and Oklahoma and has offices in Albuquerque, NM and Tucson, AZ.
Concrete Forms Deliver Highway Paving Success
Recently, Meridian has been involved in a project to widen and improve a 10-mile stretch of U.S. Highway 54 north of Tularosa, NM. The firm is constructing 14 box culverts for the widened and relocated highway, along with approximately 1,500 feet of wall barriers along the edges of the box culverts.
To pour these 42” high barriers, Meridian is using custom-designed steel concrete paving forms made by Metal Forms Corporation, a Milwaukee-based specialist in designing and manufacturing forms, screeds, stakes and other equipment for the concrete construction industry.
Working with the contractor, Metal Forms designed special forms that can be set up for the double-sloped parapet walls on this project but also adjusted easily for future bridge projects that may require a single-slope design. Project Estimator Michael Martinez explains, “I worked with Metal Forms to design them so we could use them for two types of wall barrier jobs.” He notes that Meridian owns 200 feet of the 10- foot long forms.
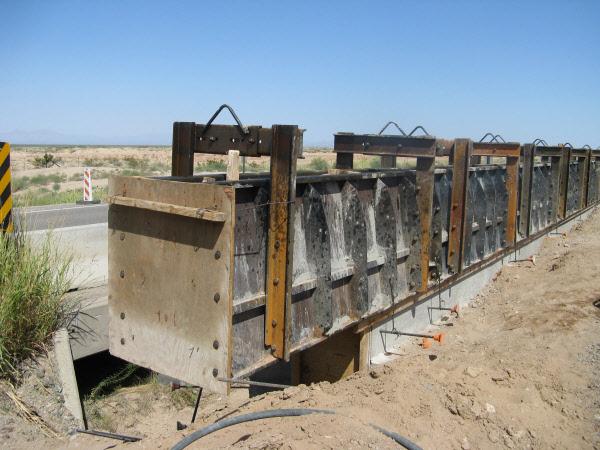
Compared to the alternative of using wood forms, the metal concrete forms save a considerable amount of time. Not only are they easier to set up, but they can be removed more quickly and re-set at the next location. Martinez points out, “We can gang-lift both sides at the same time. If we used wood forms, we would have to strip each side separately, and we couldn’t re-use them.” The metal forms also provide a higher quality end product with much less finishing, which also saves time. According to Martinez, the finish when the forms are removed is smoother and of higher quality than if wood forms were used.
On the job, once a box culvert has been completed, the forms are set in place with internal rebar along their length and dowel sockets at the ends where transition sections will be added. Because the sites where they are used are located intermittently along the 10-mile jobsite, pouring typically is done in small batches at one or two locations at a time. After the 4” slump mix has been poured and finished, the forms are easy to loosen and remove once the concrete has set so they can be moved to the next location.
Concrete Paving Forms Withstand the Elements
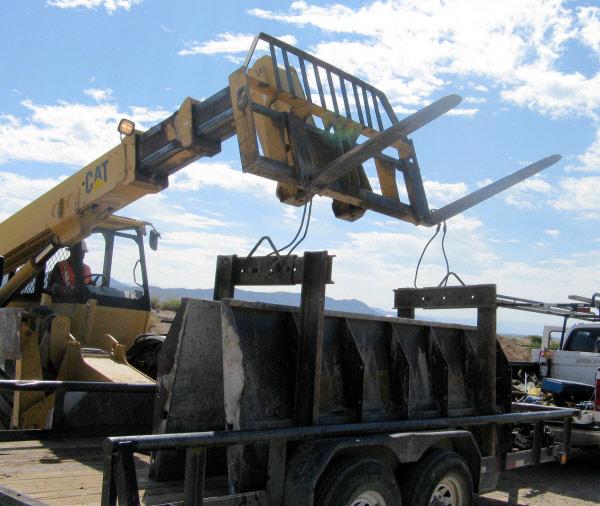
Pouring concrete in 90 degree temperatures at locations far from ready-mix plants poses special challenges. According to one authority, specifications in New Mexico call for concrete to be placed within an hour when the temperatures are above 90 degrees. To extend this time window, suppliers typically add a “recovery” chemical that slows the reaction, effectively putting the concrete to sleep. In some cases ice may be added at the plant as well. NM DOT inspectors check each batch on the jobsite for slump, air entrainment and other characteristics before approving a pour.
Martinez says they typically pour about 100 feet of the barriers at a time on this job. He adds, “When we are finished, we don’t break the forms down. We just loosen them, lift them off with a forklift and take them down the road to re-set them at the next location. This helps increase productivity, he points out.
As a result of Metal Forms working together with Meridian to meet its needs, the company has a set of metal concrete forms that not only are paying off on this job but will continue to provide higher productivity and quality on future projects as well.